Maintenance des flottes mixtes : quand opter pour la sécurité s’avère coûteux
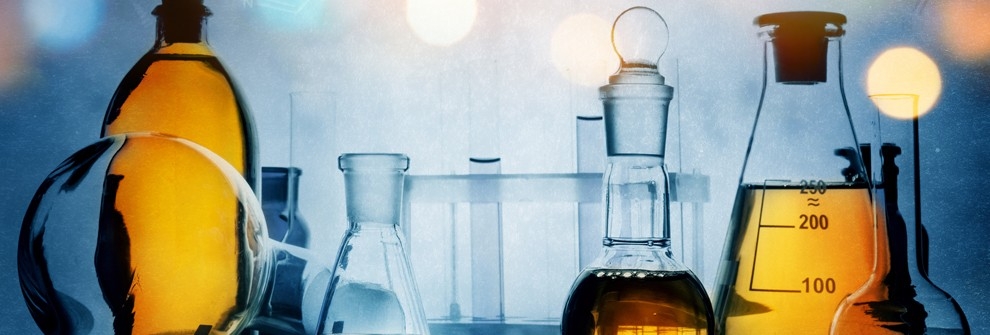
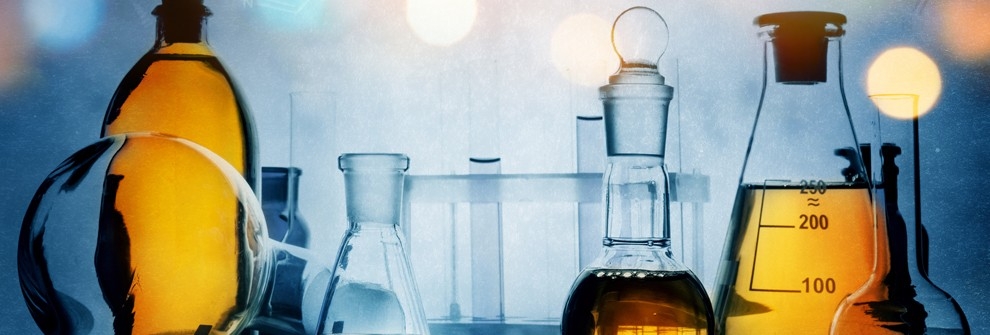
Lorsque l’on discute avec les responsables de la maintenance des équipements de construction, on comprend que les flottes mixtes sont devenues la norme. Pour expliquer le fait qu'ils ne soient plus fidèles à un constructeur en particulier, beaucoup citent comme principales raisons la pression interne au niveau des coûts et la qualité variable des équipements.
Les flottes mixtes peuvent permettre de réduire les coûts et parfois d’améliorer les performances. Pour cela, elles impliquent de faire des concessions, la principale étant un planning de maintenance bien plus complexe. Les intervalles de maintenance et d’entretien ainsi que les exigences et les besoins en matière de lubrifiants varient d’un constructeur à l’autre. La maintenance devient alors vraiment compliquée.
Comment s’en sortir ? De nombreux responsables adoptent une approche traditionnelle à l’égard des plannings de maintenance et des intervalles entre les vidanges d’huile en essayant de définir un même intervalle pour l’ensemble de la flotte. Cela entraîne cependant trop souvent des vidanges d’huile et des cycles d’entretien plus fréquents que nécessaire et non conformes aux recommandations des constructeurs. Cette approche traditionnelle est selon eux une garantie bon marché, qui supprime la nécessité de procéder à des analyses d’huile régulières.
Ce que ces responsables ne comprennent pas, c’est que l’analyse de l’huile ne porte pas seulement sur l’huile. Elle permet d’identifier de nombreux types de problèmes au niveau de l’équipement : y a-t-il un phénomène de dilution du carburant, de contamination par la saleté, de fuite du liquide de refroidissement ou un autre problème qui pourrait avoir un impact sur les performances ? L’analyse de l’huile vous permet d'anticiper et éventuellement d’éviter les pannes imprévues de l’équipement.
En définissant le même intervalle de maintenance pour l'ensemble des véhicules de votre flotte et en supprimant les analyses d'huile, vous risquez d'augmenter les coûts de main-d’œuvre et de matériaux. Quant au risque de panne catastrophique au niveau d’une machine en particulier, il peut augmenter de 11 %.
Prenons un équipement couramment utilisé, tel qu’une décapeuse. Le coût des vidanges d’huile, qui comprend le coût de l’huile, des filtres, de l’huile usagée et de la main-d’œuvre, est d’environ 1 540 dollars par an. Si nous partons du principe que votre flotte compte 100 machines similaires qui bénéficient de quatre vidanges par an, les vidanges vous coûtent 154 000 dollars par an. Le fait de procéder régulièrement à des analyses de l’huile permet de supprimer au moins une vidange par machine et par an en moyenne. En d’autres termes, sans analyse régulière de l’huile, vous dépensez inutilement chaque année 38 500 dollars. Sans compter les périodes d'immobilisation de vos équipements qui peuvent être bien plus coûteuses que les économies réalisées sur les coûts de matériaux.
Sans analyse régulière de l’huile, vous réduisez également la possibilité d'anticiper les pannes d’équipement courantes. Par exemple, 40 % des pannes moteur sont liées à la contamination du système de refroidissement, ce qu’une analyse d’huile peut facilement détecter. À combien s’élèvent les coûts de remplacement ou de réparation d’un moteur endommagé par du liquide de refroidissement ? Disons 90 000 dollars en moyenne. Généralement, on compte une réparation imprévue par an, soit 90 000 dollars. Ajoutez cette somme aux 38 500 dollars (le prix d'une vidange par an pour vos 100 machines), vous obtenez la somme d'environ 130 000 dollars par an. Cette somme, c'est ce que vous perdez en supprimant les analyses d'huile et en fixant le même intervalle de maintenance à toutes vos machines.
Un programme de maintenance préventive complet permet de suivre facilement tous les intervalles requis par les constructeurs et de programmer la maintenance en conséquence, ce qui inclut une analyse régulière de l’huile. Cela permet de réduire la consommation de lubrifiant de 25 % en moyenne et également d’augmenter la disponibilité et l’utilisation des équipements. Vous pouvez entretenir le bon équipement au bon moment et être alerté des pannes potentielles avant qu’elles ne surviennent. Cela permet de réduire les coûts de matériaux mais également d’optimiser la productivité et le retour sur investissement de chaque véhicule ou machine.
Où le programme que vous utilisez actuellement se situe-t-il par rapport à vos attentes ?